Free Boiler Installation 2015
These boilers include stationary, portable, and traction type boilers, but not locomotive and high-temperature water boilers, nuclear power-plant boilers (see Section XI), heating boilers (see Section VI), pressure vessels, or marine boilers. Guidelines are also provided for operation of auxiliary equipment. This form may be obtained from The National Board of Boiler and Pressure Vessel Inspectors, 1055 Crupper Ave., Columbus, OH 43229 NB-365 Rev. 2 Created Date 5/5/2015 9:06:22 AM.
- Gas Boiler Installation Instructions
- Gas Boiler Installation Regulations
- Gas Boiler Installation
- Free Boiler Installation 2015 Honda
- Boiler Installation Cost
- Boiler Installation Price
The free boiler scheme has been around for a good few years now, hundreds of thousands of free boilers have been installed in to peoples homes throughout the UK and now, thanks to the UK government, the scheme has been extended until at least 2017.
If you claim the correct combination of income-related benefits, you could qualify to have a free boiler installed in to your home either completely free of charge, or heavily subsidised. When the scheme was extended in 2015’s new financial year, some changes took place the criteria was tweaked slightly.

Gas Boiler Installation Instructions
Before you apply for a free boiler grant, below are five things you should know;
- Free Boilers are available for a limited time only – The Free Boiler scheme has been extended until 2017, but there is still only a very limited pot of funding which is available. If you think you may qualify, act fast and apply as quickly as you can.
- Income limited raised to £16,010 – Last year, the limit was £15,860 if you were in receipt of Child Tax Credits, or Working Tax Credits. It has now been raised up to £16,010 which opens the scheme up to a whole new range of people.
- A/B Rated Boilers can now be replaced – Previously, the free boiler scheme did not allow installers to replace A/B rated boilers. Now, however, if your boiler is broken beyond economical repair, then you could qualify for a fully funded, free replacement.
- Funding levels have increased slightly – In recent weeks, new contracts have been rolled out to free boiler installers and the rate has increased slightly from what it was at the start of 2015. This means that if you had an assessment previously and were told you may have had to contribute a high amount to cover the installation costs, you may now be able to have the boiler installed for free, or subsidised even more.
- Nationwide Coverage – There are installers all over the country now who are able to look after the free boiler grant installation. So, no matter where you live, if you apply, you should be able to have a survey within as little as 48 hours.
Want to know if you qualify? Use this form to see if you qualify for a free boiler grant.
The intent of this brief is to provide code-related information about gas-fired boilers to help ensure that the measure will be accepted as being in compliance with the code. Providing notes for code officials on how to plan reviews and conduct field inspections can help builders or remodelers design installations and prepare construction documents, and provide jurisdictional officials with information for reviews, inspection and acceptance. Providing the same information to all interested parties (e.g., code officials, builders, designers, etc.) is expected to result in increased compliance and fewer innovations being questioned at the time of plan review and/or field inspection.
A boiler typically uses a fuel such as natural gas, propane, or fuel oil in a vented combustion chamber, much like a furnace. Whereas a furnace directly transfers heat from combustion to supply air in the air distribution unit, a boiler heats a secondary transfer fluid (typically water, but sometimes steam) that is, in turn, pumped through a radiation/convection system located throughout a building or home. The hot water can also be used to heat air via a coil and blower. Boilers are more commonly used in commercial construction than residential construction, but they may be more prevalent in residential construction in some areas of the country and in older homes. Boilers are typically between 75% and 96% efficient in the primary process of heating the water, but any un-insulated heating water piping will lower the overall efficiency of space heating.
In addition to the boiler unit, a gas-fired boiler requires a feed water supply, a boiler loop/heat delivery system (e.g., hydronic radiators or fan coil units), fuel supply piping and equipment, and a temperature control system. The chapters of the International Residential Code (IRC) that are likely relevant to the installation of a gas-fired boiler include Chapter 13, General Mechanical System Requirements; Chapter 14, Heating and Cooling Equipment; Chapter 20, Boilers and Water Heaters; Chapter 21, Hydronic Piping, and Chapter 24, Fuel Gas.
The relevant energy-efficiency sections of the 2015 International Energy Conservation Code (IECC) and IRC (Chapter 11, Energy Efficiency) that relate to gas-fired boilers include Section R403, Systems (IECC) and N1103, Systems (IRC). For existing buildings, new heating and cooling systems that are part of a remodel or alteration or an addition must comply with Section R502/N1108 with the exception of where ducts from an existing heating and cooling system are extended to an addition, duct systems with less than 40 linear feet in unconditioned spaces are not required to be tested per R502.1.1.2/N1108.1.1.2. The Energy Efficiency provisions related to hot water boilers for the 2009, 2012, and 2015 code versions have mostly remained the same except for inclusion of an outdoor setback control requirement to control the water temperature based on the outdoor temperature. This specific requirement, which was added in the 2015 version, is detailed below under the Plan Review and Field Inspection sections.
The focus of this brief is on boiler efficiency, sizing requirements, controls, combustion air, and duct and pipe insulation for the 2015 version of the IECC/IRC.
Per the 2015 IECC/IRC, Section R103.3/R106.3, Examination of Documents. The code official/building official must examine, or cause to be examined, construction documents for code compliance.
This section lists the applicable code requirements followed by details helpful for plan review regarding the provisions to meet the requirements for 'gas-fired boilers.'
Construction Documentation. Review the construction documents to identify the equipment, system controls, design, and ventilation choices to the equipment.
2015 IECC/IRC, Section R103.2/N1101.5, Information on Construction Documents.. Construction documents should include:
— Insulation materials and their R-values
— Mechanical system design criteria
— Mechanical system equipment types, sizes, and efficiencies
— Equipment and system controls
— Duct sealing, duct and pipe insulation and location
— Air sealing details
— Flashing and moisture control.
2015 IRC requirements for gas-fired boiler installations are found throughout Chapter 13, General Mechanical System Requirements; Chapter 14, Heating and Cooling Equipment; Chapter 20, Boilers and Water Heaters; Chapter 21, Hydronic Piping; and Chapter 24, Fuel Gas. This section lists the applicable IRC and IECC code sections.
General Installation Provisions. Review the construction documents for equipment installation.
— 2015 IRC, Sections M2001, General, and G2404, General. Boilers should be designed and constructed in accordance with the requirements of ASME CSD-1, 1 and gas-fired boilers should conform to the requirements listed in Chapter 24 of the IRC. Gas-fired boilers should be listed and labeled in accordance with IRC M1302.1, and should be installed:
- In accordance with the manufacturer's instructions G2408.
- On level platforms in accordance with Section G2408.4
- With proper clearances as specified in Sections G2408.4 and G2408.5
- With shutoff valves in the supply and return piping per Sections M2001.3 and G2420
- With operating and safety controls in accordance with Sections M2002 and G2421
- So openings in exterior walls are flashed in accordance with Section R703.4
- To protect the potable water supply in accordance with Section P2902
- So air intake openings are located are in accordance with Section R303.5.1
- With circuit breakers that are sized in accordance with equipment data plate per manufacturer's installation instructions and electrical connections that conform to requirements of Part VIII (Electrical) of the IRC.
- With expansion tanks that have been specified to meet minimum capacity requirements per Section M2003.1 and, M2003.2. Minimum requirements (as listed in Table M2003.2) are specified below:
Expansion Tank Minimum Capacitya for Forced Hot-Water Systems
System Volumeb Pressurized Diaphragm Type Nonpressurized Type 10 1.0 1.5 20 1.5 3.0 30 2.5 4.5 40 3.0 6.0 50 4.0 7.5 60 5.0 9.0 70 6.0 10.5 80 6.5 12.0 90 7.5 13.5 100 8.0 15.0 aBased on average water temperature of 195°F, fill pressure of 12 psig, and a maximum operating pressure of 30 psig.
bSystem volume includes volume of water in boiler, convectors, and piping, not including the expansion tank.Mounting. Verify equipment is correctly supported and installed in the structure.
— 2015 IRC, Section G2408.4, Clearance from grade. Equipment and applications supported from the ground should be level and firmly supported on a level concrete slab or other approved material extending not less than 3 inches (76 millimeters) above adjoining grade or should be suspended not less than 6 inches (152 millimeters) above adjoining grade. Such support should be in accordance with the manufacturer's installation instructions.
— 2015 IRC, Section G2408.2, Elevation of Ignition Source. Installations within a garage should have ignition source raised 18 inches from the floor, and the boiler should be protected from impact.
— 2015 IRC, Sections G2406 and G2407.2, Appliance Location. Appliances shall not be located in sleeping rooms, bathrooms, toilet rooms, storage closets, or surgical rooms, or in a space that opens only into such rooms or spaces. Appliances should be located so as not to interfere with proper circulation of combustion, ventilation and dilution air.
Equipment Controls. Review the construction documents and confirm that controls have been installed in accordance with manufacturer installation instructions, which should include control diagrams and operating instructions.
— 2015 IECC/IRC, Section R403.1/N1103.1, Controls. Each heating and cooling system should have its own thermostat. Each thermostat controlling the primary heating and cooling system should be a programmable thermostat.
Hot water boilers that supply heat to the building through one- or two-pipe heating systems should have an outdoor reset control that lowers the boiler water temperature based on the outdoor temperature per R403.2/N1103.2.Equipment Sizing. Verify that the boiler is sized based on building loads calculated in accordance with ACCA Manual J or other approved methods (IECC R403.7/IRC M1401.3 and N1103.7).
— 2015 IECC/IRC, Section R403.7/N1103.7, M1401.3, Sizing. Heating and cooling equipment shall be sized in accordance with ACCA Manual S based on building loads calculated in accordance with ACCA Manual J or other approved heating and cooling calculation methods.
Ventilation. Chapter 24, Fuel Gas, in the 2015 IRC is extracted from the 2015 edition of the International Fuel Gas Code (IFGC) and contains specific combustion air and ventilation requirements for gas-fired appliances, such as boilers. Boilers can be vented with a conventional chimney system or through a balanced flue system for direct venting through the wall. Review the construction documents and verify that the ventilation system has been installed in accordance with manufacturer installation instructions.
— 2015 IRC, Section G2407 (304), Combustion, Ventilation, and Dilution Air. The section numbers appearing in parentheses after each section number are the section numbers of the corresponding text in the IFGC. Air for combustion, ventilation, and dilution of flue gases for appliances installed in buildings should be provided by application of one of the methods prescribed in Section G2407.5 through G2407.9 of the IRC. Outdoor air should be introduced in accordance with one of the methods prescribed below:
- G2407.6 (304.6), Outdoor Combustion Air. Outdoor combustion air provided through opening(s) to the outdoors. The minimum dimension of air openings should not be less than 3 inches. Review and confirm that the construction documents specify the combustion air opening(s) meet one of the methods below.
- G2407.6.1 (304.6.1), Two-Permanent-Openings Method. Section R703.4 Flashing. Approved corrosion resistant flashing should be applied in shingle fashion to prevent entry of water into the wall cavity or penetration of water to the building structural framing components.
- G2407.6.2 (304.6.2), One-Permanent-Opening Method. Within 12 inches of the ceiling (top of enclosure) and appliance have clearances of at least 1 inch from the sides and back and 6 inches from the front of the appliance directly communicating with the outdoors or through a vertical or horizontal duct to the outdoors or spaces that freely communicate with the outdoors with a minimum free area of 1 square inch per 3000 Btu/h of total input rating of all appliances located in the enclosure and not less than the sum of the areas of all vent connectors in the space.
- G2407.9 (304.9), Mechanical Combustion Air Supply. Where combustion air is provided by a mechanical air supply system, the combustion air should be supplied from the outdoors at a rate not less than 0.35 cubic feet per minute per 1000 Btu/h of total input rating of all appliances located within the space.
— 2015 IRC, Sections M1801and G2426.1, General. Fuel-burning appliances shall be vented to the outdoors in accordance with their listing and label and manufacturer's installation instructions. Venting systems shall consist of approved chimneys or vents, or venting assemblies that are integral parts of labeled appliances.
— 2015 IRC, Section G2427.4, Type of Venting System to be Used. The type of venting system to be used should be in accordance with Table G2427.4. See the following table.
Type of Venting System to be Used
Appliances Type of Venting System (Relevant Section of IRC) - —Listed Category I appliances
- —Listed appliances equipped with draft hood
- —Appliances listed for use with Type B gas vent
- —Type B gas vent (Section G2427.6)
- —Chimney (Section G2427.5)
- —Single-wall metal pipe (Section G2427.7)
- —Listed chimney lining system for gas venting (Section G2427.5.2)
- —Special gas vent listed for these appliances (Section G2427.4.2)
Category II, III or IV appliances As specified or furnished by manufacturers of listed appliances (Sections G2427.4.1, G2427.4.2) Direct-vent appliances See Section G2427.2.1 — 2015 IRC, Section G2425, (Conventional Chimney Venting) General. Chimneys and vents should be constructed and sized in accordance with Sections G2427 and G2428. Appliance should connect to chimney flue at a point not less than 12 inches above the lowest portion of the interior of the chimney flue.
— 2015 IRC, Section R1003.18, Chimney Clearances. Any portion of a chimney located in the interior of the building or within the exterior wall of the building should have a minimum air space clearance to combustibles of 2 inches. Chimneys located entirely outside the exterior walls of the building should have a minimum air space clearance of 1 inch. The air space should not be filled, except to provide fire blocking in accordance with Section R1003.19.
— 2015 IRC Section G2427.2.1 (503.2.3), Direct-Vent Appliances. Listed direct-vent appliances should be installed in accordance with the manufacturer's instructions and Section G2427.8.
- 2015 IRC, Section G2427.8, Venting System Termination Location. The location of the venting system termination should conform to the requirements G2427.8 with specified distances from forced air inlets, windows, doors, gravity inlets, based on size of equipment, listed in G2427.8 and diagramed in Appendix C.
- 2015 IRC, Section G2427.9, Condensation Drainage. Condensate drainage system should be installed to collect and dispose of condensate from venting system.
- G2407.6 (304.6), Outdoor Combustion Air. Outdoor combustion air provided through opening(s) to the outdoors. The minimum dimension of air openings should not be less than 3 inches. Review and confirm that the construction documents specify the combustion air opening(s) meet one of the methods below.
Fuel Supply
— 2015 IRC, Section G2420, Gas Shutoff Valves. Piping systems should be provided with shutoff valves that are constructed of materials compatible with the piping and should comply with the standard that is applicable for the pressure and application as specified by ANSI/ASME2 Valve Standards. Shutoff valves should be accessible and should not be located in furnace plenums or concealed locations.
— 2015 IRC, Section G2421, Flow Controls. Line pressure regulators should be listed as complying with ANSI Z21.803 and should be accessible and installed where the boiler is designed to operate.
— 2015 IRC, Section G2422, Appliance Connections. Gas-fired boilers should be fuel supply connectors should be protected against physical damage and installed in accordance with manufacturer's instructions. The boiler should be connected to the gas supply piping system by one of the following:
- Rigid metallic pipe and fittings
- Corrugated stainless steel tubing
- Listed and labeled appliance connectors in compliance with ANSI Z21.24. 4
- Hydronic Piping and Distribution Systems. Review the construction documents and confirm the specified sizes, capacities, and R-value of insulation.
— 2015 IRC, Section M2101.Hydronic piping should be installed per M1308 and M2101, and materials should conform to Table M2101.1. Pipe and fittings should be rated for use at the operating temperature and pressure of the hydronic system. Piping Supports should be of material and strength adequate to support the piping and should be supported at intervals not exceeding the spacing specified in Table M2101.9 (see table below).
Hanger Spacing Intervals
Piping Material Maximum Horizontal Spacing (ft) Maximum Vertical Spacing (ft) ABS 4 10a CPVC (1-inch or less) 3 5 CPVC (1 ¼ inch) 4 10a Copper or copper alloy pipe 12 10a Copper or copper alloy tubing 6 10a 60 5.0 9.0 PB pipe or tubing 2.67 4 PEX tubing 2.67 4 PP less than 1-inch pipe 2.67 4 PP more than 1 ¼ inches 4 10a PVC 4 10a Steel pipe 12 15 Steel tubing 8 10a aFor sizes 2 inches and smaller, a guide should be installed midway between required vertical supports. Such guides should prevent pipe movement in a direction perpendicular to the axis of the pipe. — 2015 IRC, Section M2102.1, General. If baseboard convectors are used, they should be installed in accordance with manufacturer's installation instructions. Convectors should be supported independently of the hydronic piping.
— 2015 IECC, Table R402.1.2/IRC, Table N1102.1.2, Slab R-value and Depth and Section M2103, Floor Heating System. Radiant floor heating systems (heated slabs) shall have a thermal barrier.
- Table R402.1.2/N1102.1.2, Slab R-value and depth, footnote d. Heated slabs should include an additional minimum insulation R-value of 5 to the slab edge. Insulation depth should be the depth of the footing or 2 feet, whichever is less in Climate Zones 1 through 3 for heated slabs.
- M2103.2.1, Slab-on-grade. Radiant piping used in slab-on-grade applications should be insulated to a minimum R-value of 5 installed beneath the slab.
- M2103.2.2, Suspended floor. Suspended floor applications, insulation should be installed in the joist bay cavity serving the heating space above and should be insulated to a minimum R-value of 11.
- Flashing/Moisture Control. Verify that the design and specification of the weather-resistive covering, water-resistive barrier, flashing, and drainage are specified on the construction documents and meet applicable codes.
— 2015 IRC, Section R303.6, Outside Opening Protection. Air exhaust and intake openings that terminate outdoors should be protected with corrosion-resistant screens, louvers, or grills having a minimum opening size of ¼ inch (6 millimeters) and a maximum opening size of ½ inch (13 millimeters), in any direction. Openings should be protected against local weather conditions. Outdoor air exhaust and intake openings should meet the provisions for exterior wall opening protection in accordance with this code.
— 2015 IRC, Section R703.4, Flashing. Approved corrosion-resistant flashing should be applied shingle-fashion to prevent water from entering wall cavities or from penetrating into building structural framing components. Self-adhered flashing must comply with AAMA5 711. Fluid-applied membranes used as flashing in exterior walls should comply with AAMA 714. The flashing should extend to the surface of the exterior wall finish or to the water-resistive barrier. For this code, approved corrosion-resistant flashings should be installed at all wall and roof intersections.
- Potable Water System Protection. Verify that potable water connections to the equipment are correct.
— 2015 IRC, Section P2902.1, General. A potable water supply system should be designed and installed as to prevent contamination from non-potable liquids, solids, or gases being introduced into the potable water supply. Connections should not be made to a potable water supply in a manner that could contaminate the water supply or provide cross-connection between the supply and a source of contamination except where approved methods are installed to protect the potable water supply. Cross-connections between an individual water supply and a potable public water supply should be prohibited.
- Mechanical System Ducts. If ducts are employed as part of the installation, review the construction documents and confirm the specified R-value of insulation for air ducts.
— Insulation
- 2015 IECC/IRC, Section R403.4/N1103.4. Mechanical system piping insulation.Mechanical system piping capable of carrying fluids >105°F or <55°F must be insulated to at least R-3.
R403.4.1/N403.4.1 Protection of piping insulation. Piping insulation exposed to weather must be protected from damage caused by sunlight, moisture, equipment, and wind. The protection cannot be provided by adhesive tape.
- 2015 IECC/IRC, Section R403.3.1/N1103.3.1, Ducts. Insulation.
- Supply and return ducts installed in attics should be insulated to R-8 if ducts are ≥3 inches in diameter or to R-6 if ducts are <3 inches in diameter.
- Supply and return ducts installed in other portions of the building should be insulated to R-6 if ducts are ≥3 inches in diameter R-4.2 if ducts are <3 inches in diameter.
Exception:
Ducts or portions thereof located completely inside the building thermal envelope.
- Duct Leakage/Air Sealing. Review the construction documents and confirm that the appropriate level of duct sealing is used based on the code to be applied. Be aware that current codes require duct tightness beyond just mechanical sealing of joints and that leakage be verified via field testing, and supporting documentation be provided to the code official. The code official should consider transmitting the jurisdictional requirements during the plan review phase.
— 2015 IECC/IRC, Section R403.3.2/N1103.2.2, Sealing. Ducts, air handlers, and filter boxes should be sealed. Joints and seams should comply with the International Mechanical Code (IMC) or IRC, Section M1601.4.1, as applicable.
Exceptions:
- Application of air-impermeable spray foam products should be permitted without additional joint seals.
- For ducts having a static pressure classification of less than 2 inches of water column (500 Pa), additional closure systems should not be required for continuously welded joints and seams, and locking-type joints and seams of other than the snap-lock and button-lock types.
Existing Buildings and Replacement. New boilers that are part of an addition shall comply with new construction sections of the code. An exception is, when ducts are used as part of an existing heating and cooling system and are extended to an addition, a duct system with less than 40 linear feet in unconditioned spaces does not need to be tested. Replacement boilers should be installed in accordance with relevant standards including ACCA Standard 5: HVAC Quality Installation,6 Specification and the ACCA's Technician's Guide for Quality Installations, and ACCA Standard 9: HVAC Quality Installation Verification Protocols.7
1American Society of Mechanical Engineers (ASME) Combustion Side Control (CSC) – 1
2American Society of Mechanical Engineers (ASME) and American National Standard Institute (ANSI) as directed in Table G2420.1.1 of the IRC.
Gas Boiler Installation Regulations
3ANSI Z21.80 – 'Line pressure regulators'. American National Standard Institute. http://www.ansi.org/.
4ANSI Z21.24 – 'Connectors for gas appliances'. American National Standard Institute. http://www.ansi.org/.
Gas Boiler Installation
5AAMA – American Architectural Manufacturers Association L (Underwriters Laboratory) is a global independent safety science company that certifies, validates, tests, inspects, audits, and advises and trains.
6ACCA Standard 5: http://www.energystar.gov/ia/home_improvement/home_contractors/qispec.pdf
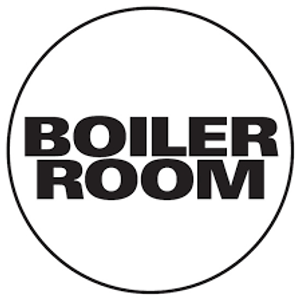
7ACCA Standard 9: http://www.energystar.gov/ia/home_improvement/home_contractors/QI_Verification_Protocols.pdf
Per the IECC, Section R104, Inspections. Construction or work for which a permit is required is subject to inspection. Construction or work is to remain accessible for inspection purposes until the inspection is complete and the work approved. Required inspections include footing and foundation, framing and rough-in work, plumbing rough-in, mechanical rough-in, and final inspection.
Per the IRC, Section R109, Inspections. The wording is somewhat different in that, for onsite construction, from time to time the building official, upon notification from the permit holder or his agent, can make, or cause to be made, any necessary inspections. Further details are provided for inspections regarding the foundation, plumbing, mechanical, gas and electrical, floodplain, frame and masonry, and final inspection. Any additional inspections are at the discretion of the building official.
Free Boiler Installation 2015 Honda
This section provides details for inspecting to the specific provisions for gas-fired boilers where one or more specific type of inspection per the IECC or IRC may be necessary to confirm compliance. The mechanical rough-in and/or final inspection would be most likely the inspections to confirm code compliance for 'gas-fired boilers.'
Inspections should provide verification in the following areas:
- Boiler is properly located and mounted, and connections are made per approved construction documents. Proper clearances are maintained for hazardous or noxious fumes.
- Verification that appropriate thermostats and outside-air heating-water-reset controls are installed per the approved construction document.
- Confirmation that shutoff valves are readily accessible and that piping is properly installed and insulated, including pipe hangers at correct spacing.
- All intake and exhaust openings are properly located and flashed to prevent moisture incursion.
- If employed, radiant system is installed in accordance with manufacture's installation instructions and R-values of insulation meet the approved R-value per construction documents.
- If ducts are used in the installation, verify that joints and seams in ductwork are properly sealed, and the duct tightness report is complete and has been submitted per jurisdictional requirements.
- Verify that pumps are listed and labeled and conform to approved construction documents.
Boiler Installation Cost
This section provides additional information and helpful resources
Boiler Installation Price
- To ensure optimal boiler installations, refer to the following guides:
— ACCA Standard 5: HVAC Quality Installation, Specification: https://www.energystar.gov/ia/home_improvement/home_contractors/qispec.pdf
— ACCA Technician's Guide for Quality Installation: A Compendium to ANSI/ACCA 5 Q1-2010 HVAC Quality Installation Specification, Air Conditioning Contractors of America, 2008.
— ACCA Standard 9: HVAC Quality Installation Verification Protocols: http://www.energystar.gov/ia/home_improvement/home_contractors/QI_Verification_Protocols.pdf
— ACCA Manual J: Full Residential Load Calculation: https://basc.pnnl.gov/resources/acca-manual-j-residential-load-calculation
- For additional information and illustrations on boiler controls, see:
— Boiler Reset Control Overview (ESC): http://cleanboiler.org/learn-about/boiler-efficiency-improvement/efficiency-index/boiler-reset-control/
— Controls Guide for gas-Fired Boilers: https://basc.pnnl.gov/resource-guides/gas-fired-boilers#block-views-guide-static-blocks-block-1
— Illustrations of boiler reset controls can be seen at: http://cleanboiler.org/learn-about/boiler-efficiency-improvement/efficiency-index/boiler-reset-control/
- Boilers, Baseboard Radiation, Finned Tube (Commercial) Radiation, and Indirect-Fired Water Heaters:http://www.ahrinet.org/App_Content/ahri/files/Certification/I=B=RBaseboardRadiation.pdf
Author: Air-Conditioning Heating and Refrigeration Institute
Publication Date: April 2009 - Case Study: DOE Zero Energy Ready Home Case Study: BPC Green builders, New Fairfield, Connecticut: http://energy.gov/sites/prod/files/2014/10/f18/BA_ZeroEnergyReady_BPC_GreenBuilders_062214.pdf
Author: PNNL
Publication Date: September 2013 - Case Study: DOE Zero Energy Ready Home Case Study: Ferguson Design & Construction, INc. Sagaponack, NY. http://energy.gov/sites/prod/files/2014/10/f18/BA_ZeroEnergyReady_Ferguson%20Design_062314.pdf
Author: PNNL
Publication Date: September 2013 - Technology Solutions Case Study: Opti8mizing Hydronic System Performance in Residential Appliacations, Ithaca, New York.http://energy.gov/sites/prod/files/2014/02/f7/case_study_hydronic_system_homes.pdf
Author: CARB
Publication Date: November 2013 - 'Connection of Vent Connectors to Chimneys for Liquid and Solid Fuel Appliances.' Home Owners Network, Online at: https://www.homeownersnetwork.com/booktopic/connection-vent-connectors-chimneys-liquid-solid-fuel-appliances/#more-2695.
- Control and Safety Devices for Automatically Fired Boilers: https://www.asme.org/products/codes-standards/csd1-2012-controls-safety-devices-automaticall-(1)
Author: American Society of Mechanical Engineers
Publication Date: January 2012